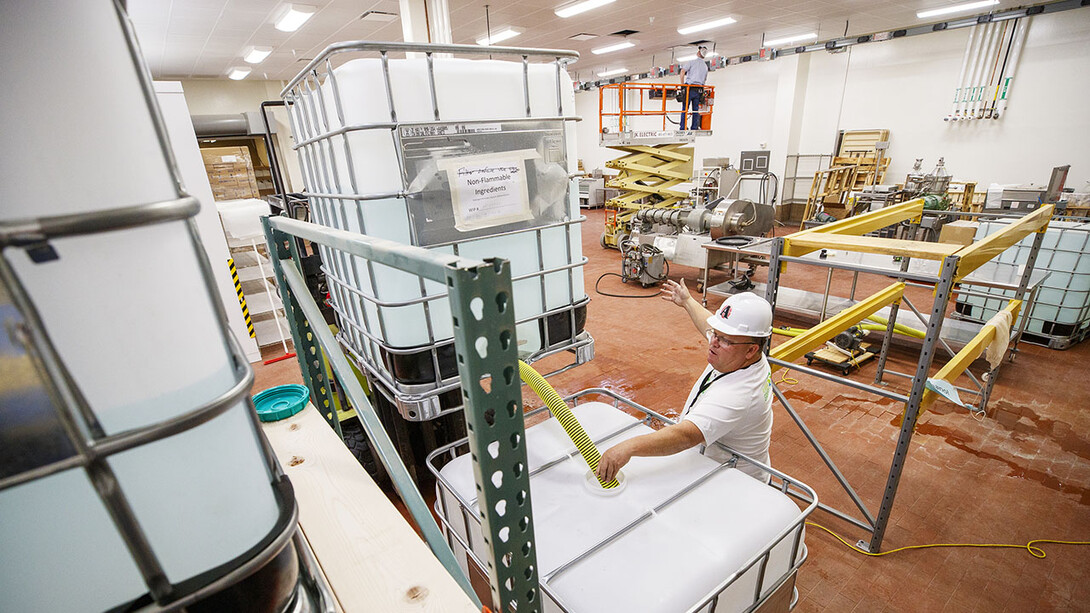
In mid-March, when personal protective equipment and hand sanitizer were scarce, the University of Nebraska–Lincoln’s Nebraska Innovation Campus helped address those needs.
The efforts have rippled across Nebraska and the United States. To date, hundreds of communities and thousands of individuals have benefited from the expertise and innovation found at NIC.
Staff and faculty affiliates of Nebraska Innovation Studio designed and is manufacturing face shields in-house. NIS staff also designed a quick way to produce PPE gowns, and coordinated the army of volunteers to make the gowns.
“This may be the reason Innovation Studio exists — for people to come together to make things that help others — and this is the moment it was born for,” said Shane Farritor, Lederer Professor of Engineering and executive chairman of the studio’s board of advisers, during a March interview.
Nebraska Innovation Campus’ Food Processing Center served as the manufacturing hub of hand sanitizer, in partnership with ethanol producers across the state.
Leaders at both the Food Processing Center and Innovation Studio said the projects are ongoing and have been a success.

Here’s a closer look at the impact of the projects:
Face shields
One of the first endeavors to get under way was the manufacturing of face shields. The project was started when hospital administrators reached out to Innovation Studio to find out if they could make 3-D printed parts for the shields.
By establishing partnerships with the Terry Research Lab in the College of Engineering and local businesses including Firespring, Midlands Packaging, Lincoln Tool and Design, Snap On and Virtual Incision, Innovation Studio was able to mass produce entire face shields, and at a much faster rate than 3-D printing would allow.
The team at NIS is producing about 45 shields per hour. As of May 14, 22,000 face shields have been produced and shipped to more than 45 Nebraska communities, to five states and a hospital in New York City.
Face shields have also been supplied to many Nebraska dental offices, allowing them to safely re-open and resume care for their patients.
“Dentists told us that without our face shields, they wouldn’t have been able to reopen May 4,” David Martin, director of Nebraska Innovation Studio, said.

Hand sanitizer
In mid-March, Hunter Flodman, assistant professor of practice in chemical and biomolecular engineering at Nebraska, saw the need for additional manufacturing of hand sanitizer and partnered with the Nebraska Ethanol Board to come up with a solution.
Since the first initial run April 5 at the Food Processing Center on Nebraska Innovation Campus, more than 60,000 gallons of hand sanitizer have been produced, with more than 750 recipients, in Nebraska and beyond.
State agencies, hospitals, first responder groups, physicians’ offices, nursing homes, childcare centers, dentists’ offices, salons and other essential businesses have all received product as needed, said Terry Howell Jr, executive director of the Food Processing Center.
Flodman and Howell noted that the project would not be possible without the support of Green Plains Inc. and KAAPA Ethanol, who are donating ethanol for the project. Also, BASF, Cargill and Syngenta are providing other required chemicals. The College of Engineering, the Institute of Agriculture and Natural Resources, University Operations and Print and Mail Services also partnered on the project.
There is no sign of slowing. The Food Processing Center will continue to make hand sanitizer, projecting production of more than 100,000 gallons by early June, including 21,000 gallons for use at the university as campuses re-open.
Disposable protective gowns
The Lincoln-Lancaster County Health Department heard about the face shield project and reached out to Innovation Studio to see if protective gowns could be made. Studio manager Jerry Reif made some prototypes and worked with the Lincoln Fire Department to select the best design.
Staff at NIS made 150 gowns in-house, but quickly needed additional volunteers and space, Reif said. He worked with the health department to establish a partnership with Lincoln Public Schools and recruit community volunteers to cut and assemble the gowns.
To date, these efforts have led to more than 1,500 gowns distributed to local fire departments, EMTs and other first responders.