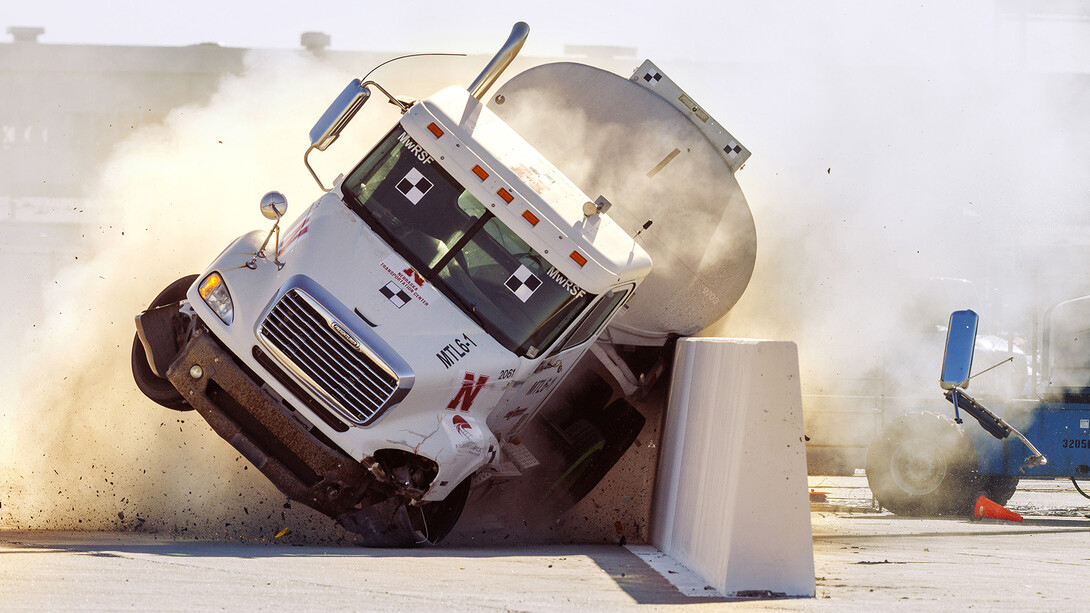
Researchers from the Midwest Roadside Safety Facility conducted a rare tractor-tanker crash Dec. 8 to test how a newly designed and significantly shorter concrete roadside barrier performs in a crash.
The test at the facility’s Outdoor Proving Grounds on the western edge of the Lincoln Municipal Airport was the first in the United States in more than 30 years for a Manual for Assessing Safety Hardware (MASH) Test Level 6 truck (one pulling a tanker and not a box trailer), according to Cody Stolle, research assistant professor at the University of Nebraska–Lincoln.
The primary purpose of the event was to test a newly designed 62-inch tall concrete roadside barrier’s performance when it is contacted by a fully loaded tractor-tanker vehicle.
For the past decade, Midwest Roadside Safety Facility Director Ron Faller and a team of researchers — including Stolle, Joshua Steelman and engineering graduate students — have been designing a thinner, shorter barrier that could lead to the first change in national standards in many decades. Currently, the standard roadside barrier to handle MASH TL-6 trucks is 90 inches tall, and the last test was in the late 1980s at the Texas Transportation Institute.
Computer simulations showed that at the new height, Stolle said, more of the tanker would roll over the top of the barrier but that the barrier would be tall enough to “upright the vehicle and prevent it from other potentially dangerous outcomes — like going over on its side or rupturing the tank and causing a large spill on the roadway.”
The vehicle is captured and redirected in less than 1 second, Stolle said.
The tractor — a 2010 Freightliner Columbia — was pulling a 1997 LBT T4249 tanker-trailer with a capacity of 9,400 gallons, but loaded with only 7,000 gallons of water, Stolle said. That brought the weight of the vehicle to about 80,000 pounds, or the maximum weight allowed on interstate highways.
The vehicle was hooked up to a cable system and pulled to 50 mph by another vehicle along the tarmac. At a designated point, the cable system was released, and the vehicle’s momentum carried it toward the concrete barrier constructed for the test.
The vehicle struck the barrier at 15 degrees, recreating the “practical worst-case scenario,” Stolle said.
The barrier test went exactly as predicted.
“For the purposes of containment, this test was phenomenal,” Stolle said. “This would have prevented the vehicle from penetrating past that line and that barrier into opposing traffic or off of a bridge. The barrier performed exactly as it should.”
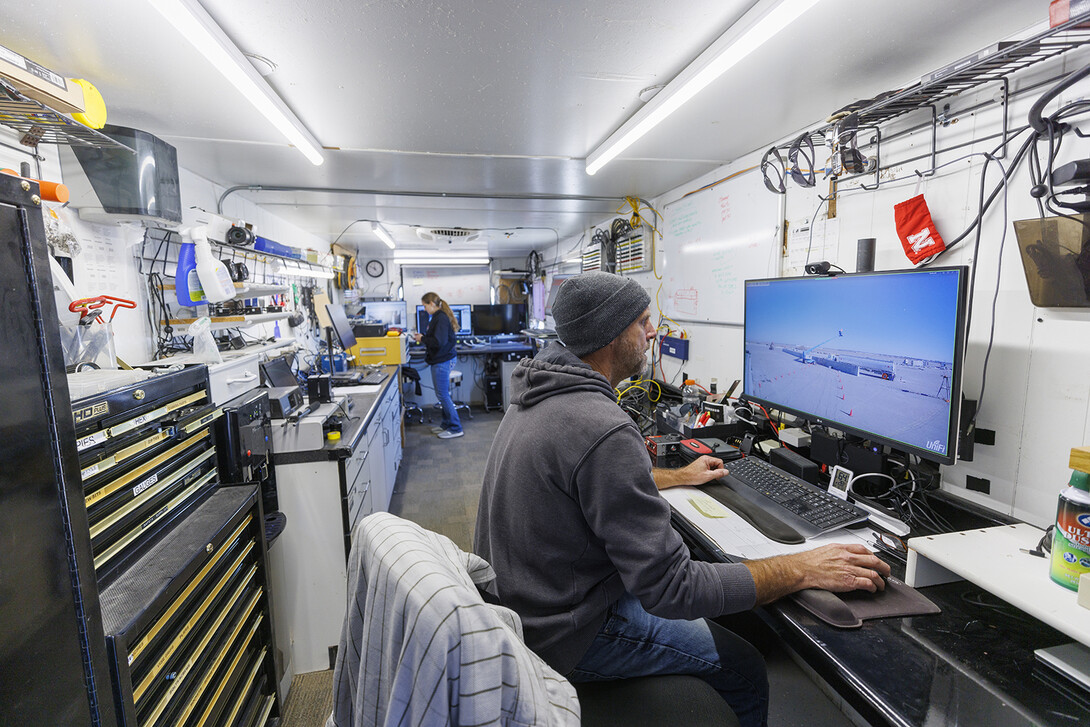
The research team will analyze the crash data as it becomes available and will then work with transportation departments to get the design accepted as a standard design. Once that is done, the bid letting process for road installation would begin. That process could take six to 18 months, Stolle said.
Many state departments have expressed interest in the barrier, Stolle said, and “citizens could see this design on the road in 12 months.”
The Midwest Roadside Safety Facility prepped and painted the tanker and outfitted the tractor with some technology to make the crash test possible, including:
A remote braking system that was operated remotely and enabled researchers to begin slowing the truck within a quarter-second after it impacted the barrier.
An industry-standard, fifth-wheel attachment that connected the tractor and tanker, which Stolle said was to lessen the chances of mechanical problems in the test.
A guidance system installed on the tractor’s passenger side — the side opposite of the barrier — allowing the researchers to guide the vehicle up to impact. The barrier was configured as a median barrier, and impact occurred on the vehicle’s left side.
Learn more about the Midwest Roadside Safety Facility.
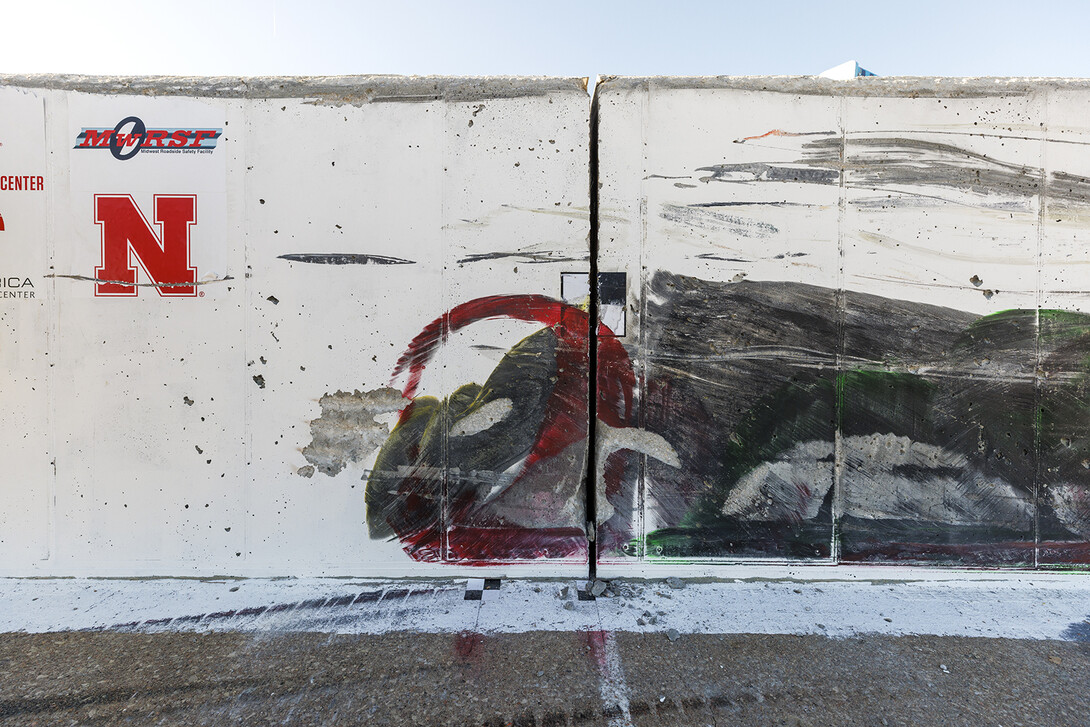