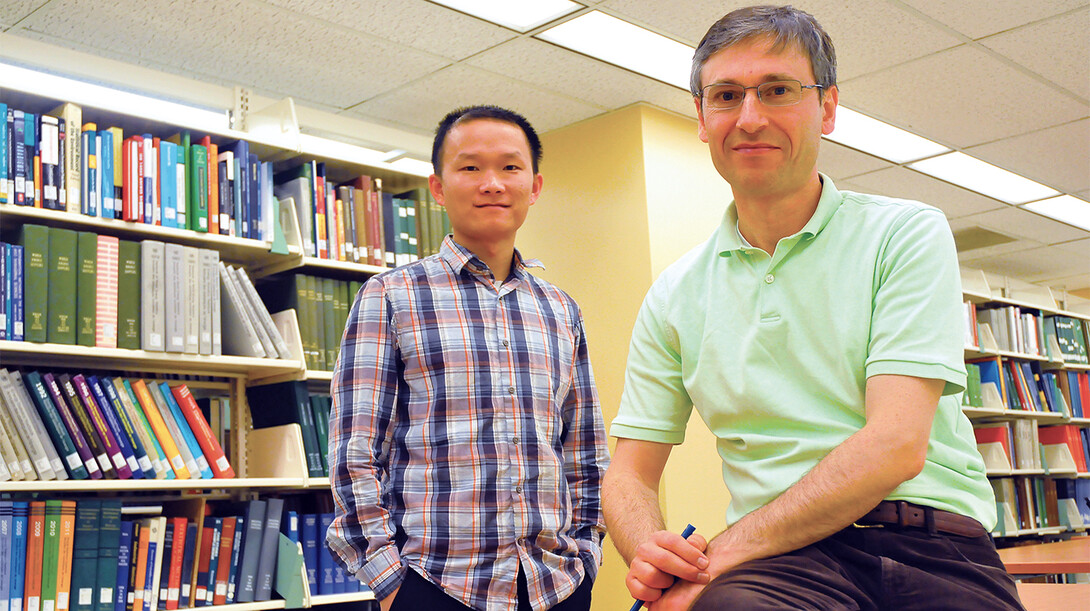
UNL engineers have developed a model that literally looks beyond the surface of corrosion to better predict its spread within the roads, bridges, ships and aircraft commonly afflicted by it.
The model’s unique capabilities could allow engineers to more precisely forecast catastrophic structural failures and design materials less susceptible to the widespread issue, the researchers reported.
The new model simulates the rate and profile of pitting corrosion, an especially potent form of degradation that is difficult to detect yet can ultimately trigger the collapse of an entire structure.
Corrosion typically arises from chemical interactions between a surface and a liquid solution such as seawater. True to its name, pitting corrosion specifically produces cavities that can compromise structural integrity from the inside out.
“If you can model a process, that’s a great first step in trying to improve the design of a material or structure,” said Florin Bobaru, the model’s co-creator and professor of mechanical and materials engineering. “Once you have that understanding, you can say, ‘I know this piece is corroded, but it’s going to last two more years,’ or, ‘I better replace this next month, because there’s a high potential that a crack will run through and damage the whole structure.’”
While formulating their model, Bobaru and postdoctoral researcher Ziguang Chen examined existing experimental data on corrosion in one-dimensional components such as wire. They then calibrated the parameters of their model accordingly, finding that its simulations of corrosion-related damage closely resembled the experimental outcomes.
After modifying their math and associated code, Bobaru and Chen expanded the model to replicate corrosion of two- and three-dimensional structures. The team’s model can be applied to both metallic and non-metallic materials, whether capturing the growth of rust on a steel pillar or the evolution of a pothole in a concrete street.
“People have been trying to model this for many years, but they’ve struggled because it’s difficult to track how the interface between a corroding solution and the solid material evolves over time,” Bobaru said.
These struggles stemmed in part from misconceptions of that interface, which previous research had usually conceived as a membrane separating the pristine metal surface from the corrosive solution, according to Bobaru.
Inspired by more recent atomic-scale investigations, Bobaru and Chen instead treated the interface as an initial layer of corrosion that indicated the presence of fainter but advancing degradation just beneath the surface.
“Our contribution was the modeling of this sub-surface layer as one that eventually weakens a material and could influence how potential cracks grow from there,” Bobaru said.
This distinction also freed the new modeling approach from the need to impose assumptions about how the interface moves through a material. Rather than presuppose the speed and direction of its movement, Bobaru and Chen were able to simply input basic parameters and watch the process unfold.
“I think that’s a very good thing, because what happens at the interface is a very complicated electrochemical process that goes all the way down to the atomic scale,” Bobaru said. “Outside of modeling each and every atom – which you cannot do except in very tiny regions – you cannot solve this problem computationally. That’s why we wanted to simplify this model as much as we could and let it tell us how this corrosion will happen by itself.
“You don’t want to make too many assumptions that may, in fact, be wrong. That’s what people had to do before this. Here, we don’t have to say anything except, ‘We’ll see what happens.’ And that happens to be very close to what occurs in reality. In our model, the speed of the advancing corrosion front isn’t part of the problem – it’s part of solving the problem.”
Migration and degradation
The new model essentially simulates two separate yet related processes. It first captures the corrosion that occurs via the escape of unbalanced atoms known as ions, which begin migrating from undisturbed metal to the interface of a corroded pit.
The presence of an encroaching liquid solution, such as rainwater that might cling to the surface of a bridge, accelerates the loss of ions by dissolving the metal that resides near the interface. The departing ions leave empty space in their wake, effectively poking holes in the material.
“Instead of just modeling what happens in the solution, we’re modeling the whole system – metal and solution,” Bobaru said. “Once we monitor the concentration of metal – and once it drops below a level where we know the material is dissolved — it transforms from a metal behavior to a liquid behavior. It takes ages for ions to move out through a metal — they diffuse very slowly — but in a liquid, they can move very fast. This allows the interface to move forward by itself in the model.”
The model then calculates how this diminishing concentration of ions contributes to the deterioration of a structure’s mechanical bonds – the physical linkages that help maintain its solid form.
“It tells us what concentration of ions we have to lose in order for a mechanical bond to break,” Bobaru said. “So the ion diffusion problem is coupled with the mechanical damage to the material.”
Stepping on the cracks
Long before he began exploring the finer points of corrosion, Bobaru was modeling fractures in materials such as glass. His relative inexperience with corrosion actually served him well, he said, by allowing him to take an unvarnished look at the issue.
“We came into this with almost no background,” Bobaru said. “That sometimes helps you, because you can come up with a fresh idea that people have not even thought about.”
Though the new corrosion model cannot yet simulate the fractures that result from broken mechanical bonds, Bobaru and Chen are now attempting to incorporate them.
“This is, in a sense, just a first step,” he said. “Once you have corrosion pits forming, a crack can emerge. This crack growth is influenced by corrosion, and the corrosion is influenced by the crack growth. The solution can get in there, speeding up the material degradation and potential catastrophic failure of your system. So we’re now exploring that.”
A study describing the new corrosion model appeared in the Feb. 27 online edition of the Journal of the Mechanics and Physics of Solids.