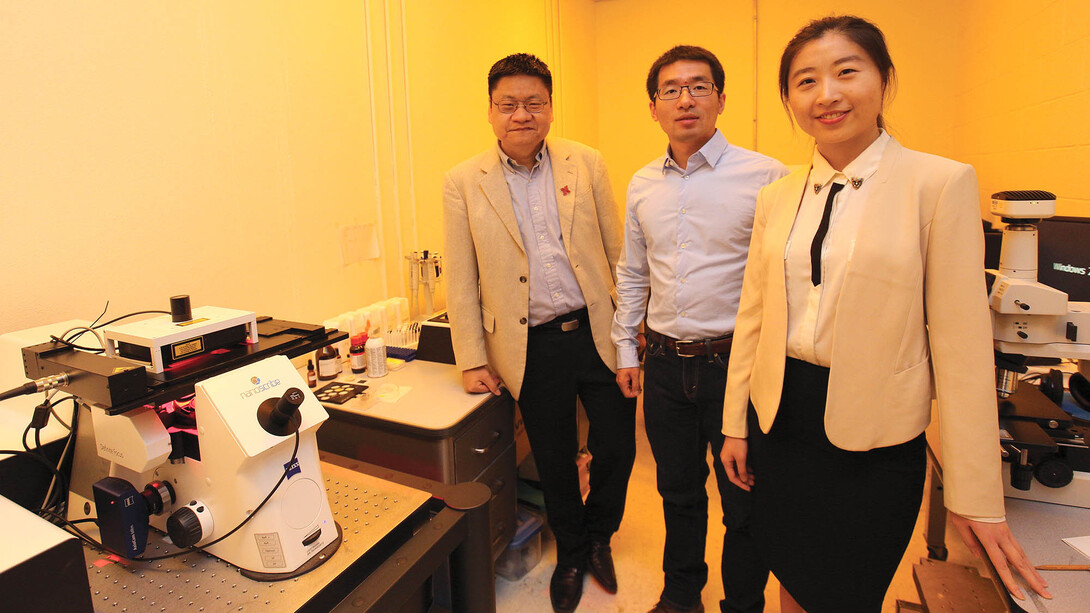
Producing the signature odors of rotten eggs, startled skunks and chopped onions should be enough to make anyone think a chemical compound stinks.
A team of electrical and computer engineers from UNL would disagree.
The engineers have found that the same compounds known for scattering people actually have a similar but desirable effect on nanoscopic carbon tubes, helping disperse them in a way that could substantially boost the performance of polymer-based technology.
With a diameter 50,000 times narrower than a human hair, carbon nanotubes have become a promising component of nanotechnology thanks to a series of appealing properties. The hollow tubes, which are made by rolling up honeycombed sheets of bonded carbon atoms, excel at conducting both electricity and heat. They also boast unparalleled tensile strength: Fibers made from the nanoscopic tubes could hypothetically extend thousands of miles without breaking.
But the nanotubes have proven unwieldy when embedded in resin-based polymers and other materials, often clumping in a haphazard fashion that diminishes the qualities that make them so prized. The way they absorb light has also limited how many nanotubes can populate resins subjected to high-intensity laser pulses that precisely sculpt the resins into microscopic three-dimensional structures.
“It’s hard to order carbon nanotubes, especially in 3-D,” said Yongfeng Lu, a Lott Distinguished University Professor of electrical and computer engineering. “When we work on devices, especially in the area of electrical engineering, we want devices that are on the nanoscale but also allow for top-down control. If (nanotubes) can be assembled in 3-D, we can see more applications. That was the starting point of this work.”
In search of a solution to the long-standing problem, Lu and his colleagues turned to the smelly class of compounds known as thiols. The researchers added dashes of thiols to a mixture that included multi-walled carbon nanotubes and a resin-based polymer. They then used ultrafast laser pulses to sculpt microscopic structures, including capacitors and gears, out of the polymer composite.
The team discovered that the resulting microstructures retained about 10 times as many carbon nanotubes as any previously reported polymer, with the nanotubes distributed evenly throughout the material. Those improvements translated to superior electrical performance: The microstructures conducted electricity at least 10 times better than other nanotube-embedded counterparts fabricated through the laser-based process.
“The thiol molecule is actually quite interesting,” said Ying Liu, a doctoral student who co-authored a recent study detailing the team’s work. “At one end, it can attach to carbon nanotubes; at the other end, it can be easily dispersed in the polymer materials we use. In this way, it’s like a bridge to link the carbon nanotubes and the polymer.”
To the team’s surprise, the nanotubes dutifully aligned in whatever direction the laser pulses moved. The resulting combination of nanotube quantity, dispersion and alignment also increased the polymer’s mechanical strength, similar to the way that rebar fortifies concrete. To help demonstrate this advantage, the researchers built two microscopic bridges: one with the carbon nanotubes, one without. Whereas the former maintained its structural integrity, the latter quickly collapsed.
“Polymers are soft materials,” Lu said. “If you apply force or heat, they start to deform. But carbon nanotubes are a very tough material that won’t deform. If we want to make a micro-electro-mechanical device, we want it to maintain its shape under extreme conditions. Carbon nanotubes can maintain those shapes.”
The researchers said their discovery could prove useful in the fabrication of conductors, transistors, resistors and other basic micro-devices that control the flow of electric current. Lu cited cellphones as one of many potential beneficiaries.
“You need three-dimensional structures with special shapes, and you also need very high electrical conductivity,” Lu said. “The systems are becoming so complicated that they need multiple microchips integrated in one system – camera modules and GPS modules and CPU modules.
“Carbon nanotubes can play a critical role. If we have control over this kind of technology, then we can put more (components) into smaller volumes.”
Lu and Liu’s recent paper appeared in the journal Advanced Materials. They co-authored the study with Wei Xiong, a former UNL postdoctoral researcher now at Huazhong University of Science and Technology (China); Lijia Jiang, doctoral student in electrical and computer engineering; Yunshen Zhou, research associate professor of electrical and computer engineering; Dawei Li, postdoctoral researcher in electrical and computer engineering; and researchers from the Beijing Institute of Technology and the Institute of Condensed Chemistry of Bordeaux (France).
The team’s research received support from the U.S. National Science Foundation.
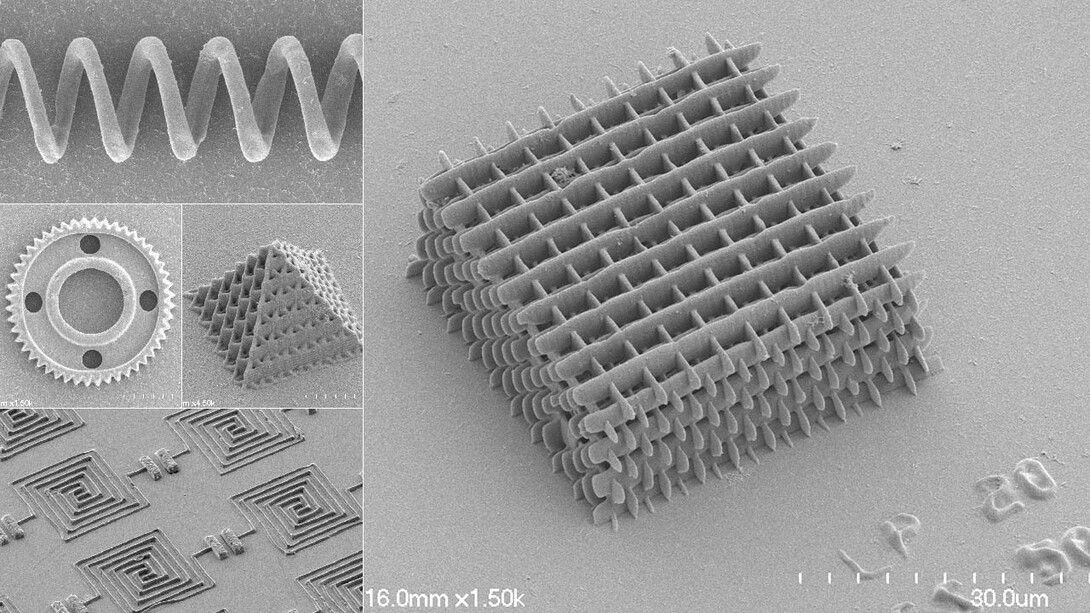